Manufacturing Simplified with ERP
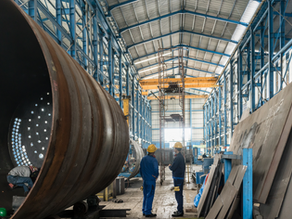
In the rapidly evolving realm of manufacturing, Managers face a plethora of challenges in effectively overseeing their operations. In recent times, the adoption of Enterprise Resource Planning (ERP) systems has emerged as a game-changing solution, offering comprehensive tools to streamline processes and enhance overall efficiency. For manufacturing companies, the benefits of embracing an ERP system are extensive, empowering them to efficiently handle quoting, work order management, time tracking and scheduling, job costing, cost management, inventory management, and invoicing. In this article, we will delve into each of these areas and explore the advantages that ERP systems bring to manufacturing operations.
Quoting
Quoting is a pivotal aspect of manufacturing operations where providing accurate and timely estimates to customers is crucial. ERP systems provide Managers with a centralized platform that automates and streamlines the entire quoting process. Integrated customer relationship management (CRM) capabilities within ERP systems enable easy access to customer data, historical quotes, and pricing information. This facilitates Managers in swiftly generating accurate quotes, reducing response time, and enhancing customer satisfaction.
Additionally, ERP systems facilitate seamless collaboration between different departments involved in the quoting process. Sales teams can effortlessly communicate with production and procurement teams, ensuring precise pricing, lead times, and material availability. The real-time visibility offered by ERP systems eliminates manual errors, minimizes the risk of miscommunication, and improves overall quote accuracy.
Work Order Management
Work order management is a critical task for operations managers in manufacturing companies. ERP systems streamline work order creation, tracking, and execution, resulting in improved productivity and reduced operational delays. By centralizing all work order information, such as required materials, labor hours, and scheduling, ERP systems provide a comprehensive overview of the manufacturing process. This enables operations managers to effectively allocate resources, optimize production schedules, and monitor progress in real-time.
With an ERP system in place, Managers can easily prioritize work orders based on customer demands, available resources, and production capabilities. The system provides alerts and notifications to ensure timely execution of work orders, minimizing bottlenecks and ensuring on-time delivery.
Moreover, ERP systems enhance visibility across the entire production floor. Through integrated shop floor control modules, operations managers gain real-time insights into machine statuses, labor efficiency, and production metrics. This empowers them to make data-driven decisions, identify areas for improvement, and optimize the overall manufacturing process.
Time Tracking and Scheduling
Efficient time tracking and scheduling are vital for Managers to optimize workforce productivity and meet production targets. ERP systems offer advanced time-tracking features that enable Managers to accurately record and monitor employee work hours, absences, and overtime. This data can be seamlessly integrated with payroll systems, simplifying the payroll process and ensuring accurate compensation.
ERP systems also provide robust scheduling capabilities, allowing operations managers to create and manage employee work schedules based on production demands and skill requirements. By aligning workforce availability with production needs, operations managers can optimize labor allocation, reduce idle time, and improve overall operational efficiency.
Real-time visibility into employee schedules and time-tracking data empowers Managers to identify bottlenecks, balance workloads, and make informed decisions regarding resource allocation. This helps in meeting production deadlines, reducing labor costs, and improving employee satisfaction.
Job Costing
Accurate job costing is essential for management to evaluate the profitability of projects and make informed decisions regarding pricing and resource allocation. ERP systems provide comprehensive job costing capabilities, allowing operations managers to track and analyze costs associated with each job or project.
By integrating with various modules, such as work orders, inventory management, and time tracking systems, ERP systems enable you to capture and allocate direct and indirect costs accurately. This includes materials, labor, equipment usage, overhead expenses, and subcontractor costs. With real-time cost tracking, Managers can closely monitor project profitability, identify cost overruns, and take proactive measures to control expenses.
Moreover, ERP systems provide detailed cost analysis and reporting capabilities. They can generate cost breakdowns, compare actual costs against budgeted costs, and analyze profitability at both the project and individual job level. This information enables companies to make data-driven decisions, identify areas for improvement, and refine cost estimates for future projects.
Cost Management
Cost management is a critical aspect of manufacturing operations as it directly impacts profitability and competitiveness. ERP systems play a vital role in enabling decision-makers to effectively manage costs throughout the organization.
With integrated financial management modules, ERP systems provide management with real-time visibility into cost data, including material costs, labor expenses, overheads, and other indirect costs. This enables management to monitor costs at various levels, from individual projects to departments and the entire organization.
ERP systems facilitate proactive cost control through features such as budgeting and variance analysis. Accountants/CFOs can set budgets, monitor actual expenses against budgeted amounts, and identify cost variances. This empowers them to take corrective actions, implement cost-saving measures, and ensure financial objectives are met.
Furthermore, ERP systems enable them to streamline procurement processes and negotiate favorable terms with suppliers. With access to comprehensive supplier and vendor information, including pricing contracts, performance data, and order history, operations managers can optimize procurement decisions, negotiate better prices, and reduce purchasing costs.
Inventory Management
Effective inventory management is crucial for manufacturing companies to meet customer demands while minimizing carrying costs. ERP systems provide robust inventory management modules that allow Managers to track inventory levels, manage replenishment, and optimize inventory control strategies.
ERP systems offer real-time visibility into inventory data, enabling operations managers to accurately monitor stock levels, identify slow-moving or obsolete inventory, and implement efficient inventory control mechanisms. By integrating with other modules such as sales, production, and procurement, ERP systems provide a holistic view of inventory requirements, enabling proactive inventory management. This reduces the risk of stockouts or excess inventory, optimizing working capital and minimizing carrying costs.
Additionally, ERP systems facilitate demand forecasting by analyzing historical data, market trends, and customer orders. Managers can generate accurate demand forecasts, allowing for improved inventory planning and reducing the occurrence of stock imbalances. This results in better customer service levels, reduced lead times, and improved overall operational efficiency.
Invoicing
The invoicing process is a critical aspect of manufacturing operations as it directly impacts cash flow and customer satisfaction. ERP systems simplify and automate the invoicing process, enabling companies to generate accurate and timely invoices.
By integrating with other modules such as sales, inventory, and finance, ERP systems streamline the invoicing workflow. When a product is shipped or a service is completed, the system automatically generates an invoice based on predefined pricing structures, discounts, and terms. This eliminates manual data entry and reduces the risk of errors.
Generating invoices based on predefined pricing structures and terms, reducing manual data entry and minimizing errors. Real-time visibility into customer payment history enables proactive credit management and better cash flow management.
Moreover, ERP systems provide real-time visibility into customer payment history, credit limits, and outstanding invoices. This enables proactive credit management, reducing the risk of bad debt and improving cash flow. Managers can easily track and follow up on overdue payments, generate statements, and reconcile customer accounts.
Implementing
Implementing an ERP system offers numerous benefits for manufacturing companies. By streamlining quoting, work order management, time tracking and scheduling, job costing, cost management, inventory management, and invoicing, you can optimize operations, enhance productivity, and drive overall business success. The centralized nature of ERP systems allows for seamless collaboration and integration across departments, enabling Management to make informed decisions based on real-time data.
From the initial quoting process to the final invoicing stage, ERP systems provide a comprehensive set of tools to streamline operations, improve accuracy, and enhance customer satisfaction. The automation and integration capabilities of ERP systems reduce manual errors, eliminate redundancy and save time, allowing companies to focus on strategic decision-making and process optimization.
By effectively managing work orders, tracking time and scheduling, and implementing job costing strategies, Operations Managers can optimize resource allocation, meet production deadlines, and ensure profitability. ERP systems provide visibility into costs, allowing companies to control expenses, refine cost estimates, and make informed pricing decisions.
Conclusion
Implementing an ERP system offers numerous benefits for manufacturing companies. From quoting to invoicing, ERP systems streamline processes, enhance visibility, and enable data-driven decision-making. By embracing ERP technology, your company can optimize resource allocation, improve productivity, reduce costs, and enhance customer satisfaction. In the fast-paced and competitive manufacturing industry, ERP systems provide a crucial advantage in driving operational excellence and achieving sustainable business growth.
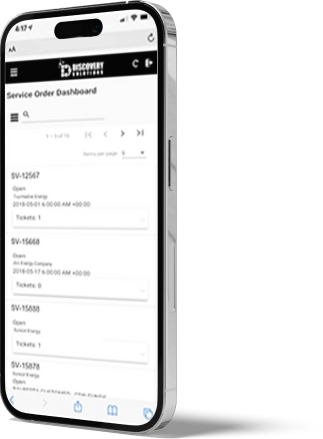
Book a Call
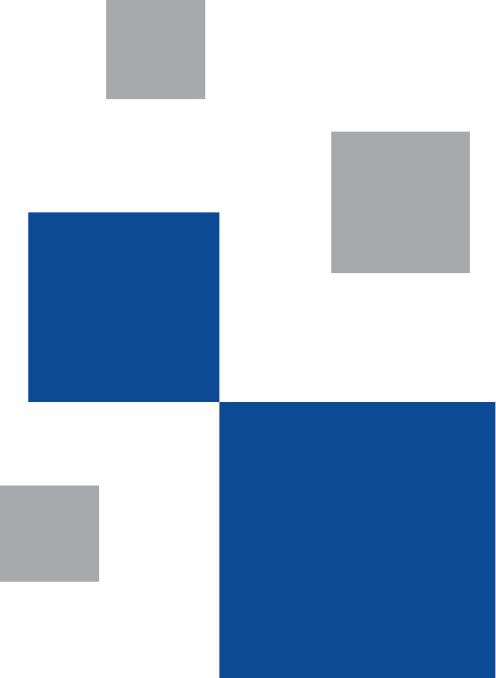